7 Key Points of Silica Sol Casting
Silica sol casting (also known as investment casting or lost wax casting) is a precision casting process widely used for manufacturing high-precision complex metal parts in industries such as aerospace, automotive, and medical. This casting process involves multiple stages with strict control over details. Below are the key aspects of each step:
Table of Contents
- 1. Mold Design
- 2. Wax Model Making
- 3. Shell Preparation (Silica Sol Binder Process)
- 4. Dewaxing
- 5. Shell Roasting
- 6. Metal Pouring
- 7. Post-Processing & Inspection
- 8.Common Defects & Solutions in Silica Sol Casting
1. Mold Design
Material selection: Choose appropriate mold materials based on the casting material (e.g., stainless steel, aluminum alloy, high-temperature alloy).
Shrinkage compensation: Account for metal solidification shrinkage (1-3%) and wax mold shrinkage (0.5-1%) by adjusting mold dimensions.
Parting surface design: Ensure smooth demolding to reduce wax mold deformation.
Casting system design: Optimize sprue, runner, and ingate to ensure smooth metal flow, preventing porosity and shrinkage defects.
2. Wax Model Making
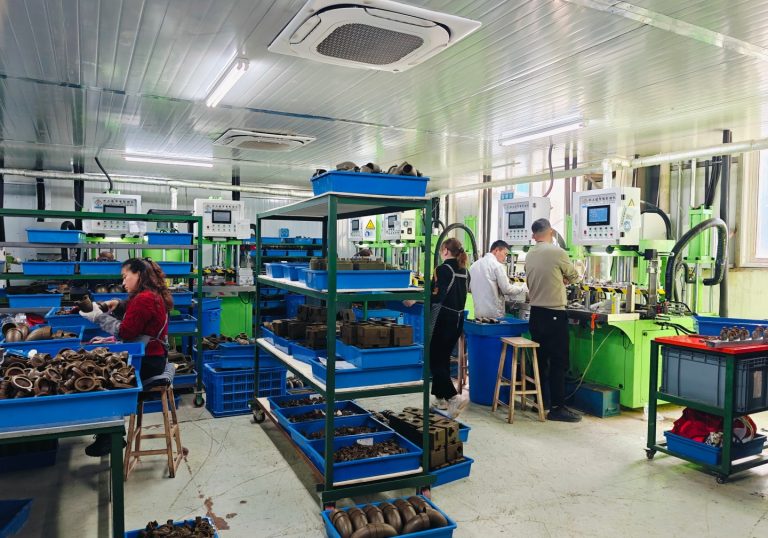
Wax material selection: Use low-temperature wax (60-80℃) or medium-temperature wax (90-120℃) with good fluidity and low shrinkage.
Wax injection parameters: Control wax injection temperature (60-80℃) and pressure (0.3-0.6MPa) to prevent surface defects like flash and depressions.
Wax model combination: Assemble wax trees with proper spacing to avoid uneven shell drying.
Wax model inspection: Check dimensional accuracy and surface quality, removing any deformed or defective wax models.
3. Shell Preparation (Silica Sol Binder Process)
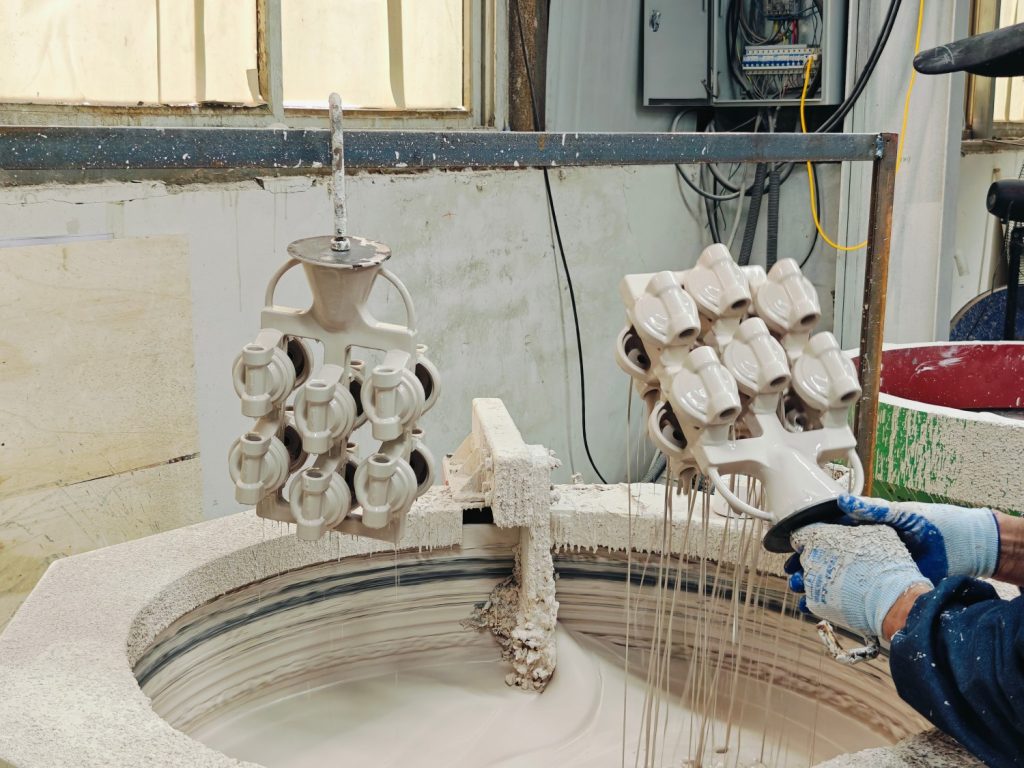
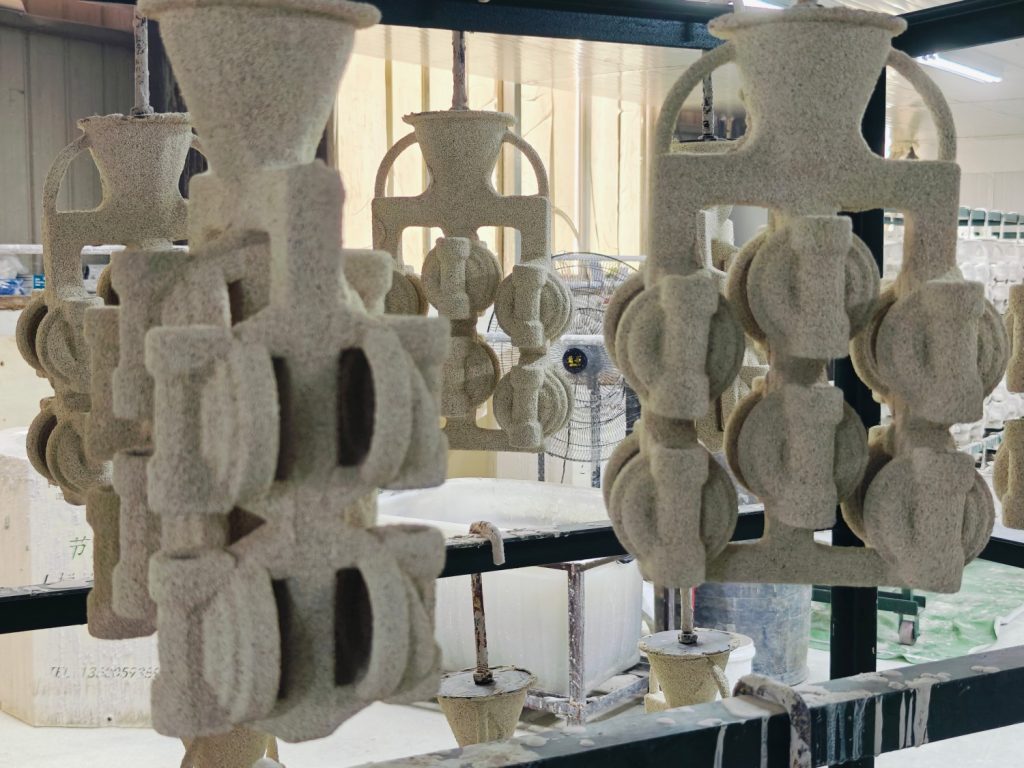
Silica sol ratio: Mix silica sol (SiO₂ colloid) with refractory powders like zircon sand or bauxite to maintain optimal viscosity (tested with coating 4 cups, 30-60s).
Coating process:
First coating layer: Use fine refractory slurry to ensure a smooth surface.
Sanding: Apply fine sand (80-120 mesh) initially, then coarse sand (30-60 mesh) in later layers for increased shell strength.
Drying conditions: Maintain constant temperature (20-25℃) and humidity (40-60%) for 12-24 hours per layer to prevent shell cracking.
Layer control: Use 6-9 coating layers, with thicker castings requiring more layers.
4. Dewaxing
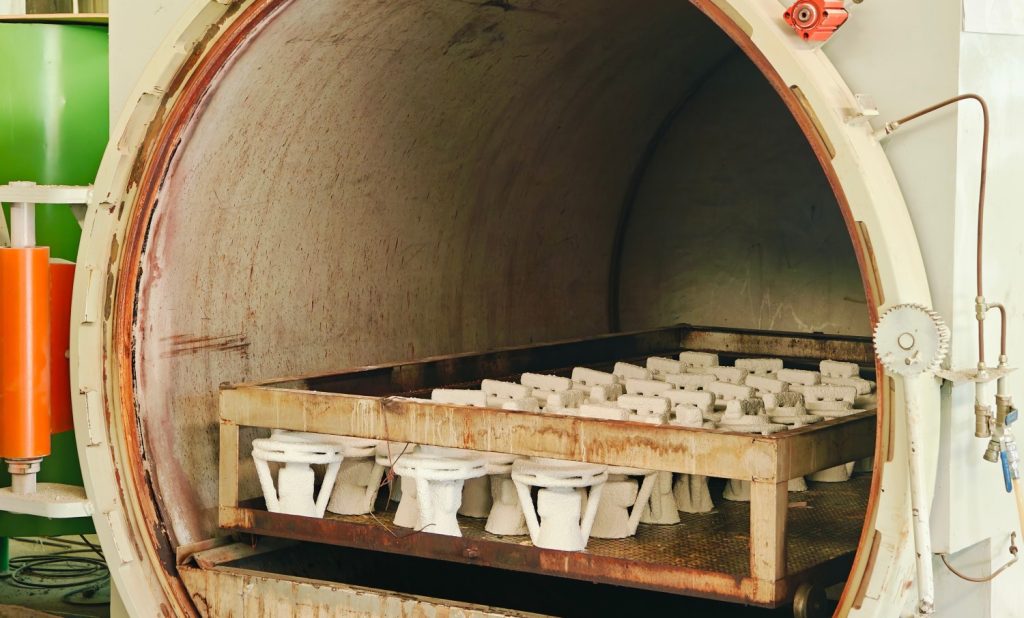
Steam dewaxing: Use high-pressure steam autoclave (0.6-0.8MPa, 150-170℃) for rapid wax removal.
Residual wax cleaning: Apply hot water or solvent cleaning to prevent carbide contamination during roasting.
Key point: Control heating rate and pressure to avoid shell cracking.
5. Shell Roasting
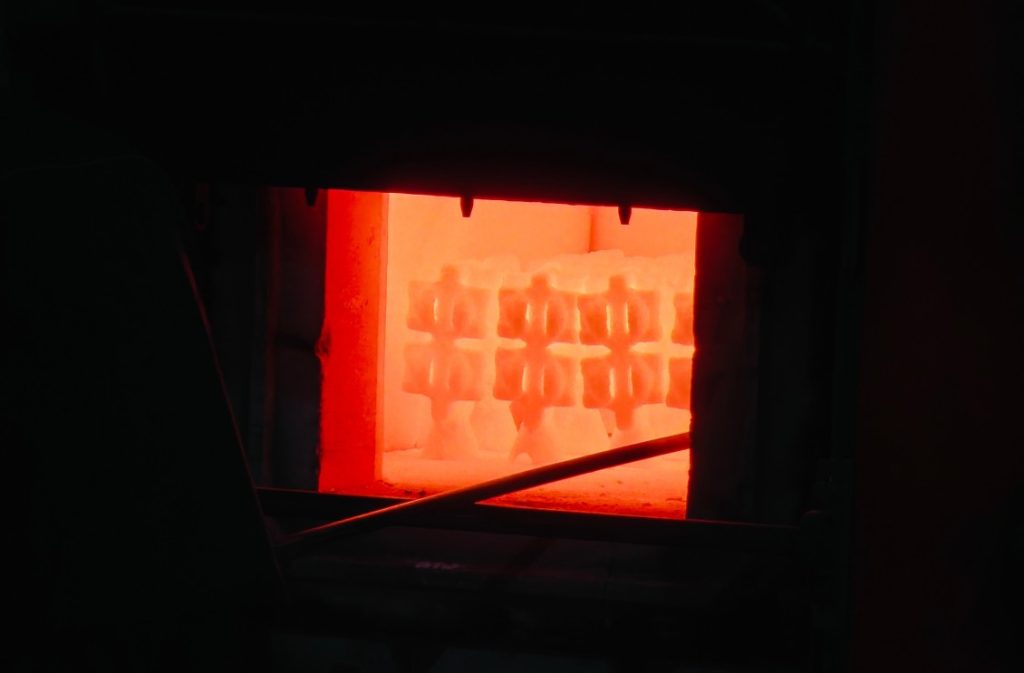
Heating curve: Gradually heat to 800-1100℃ at a rate of 100℃/h, maintaining soaking time of 2-4 hours to remove organic residues and improve shell strength.
Atmosphere control: Use oxidizing atmosphere (e.g., air) to promote carbide decomposition.
Cooling requirements: Prevent thermal shock cracking by controlled cooling.
6. Metal Pouring
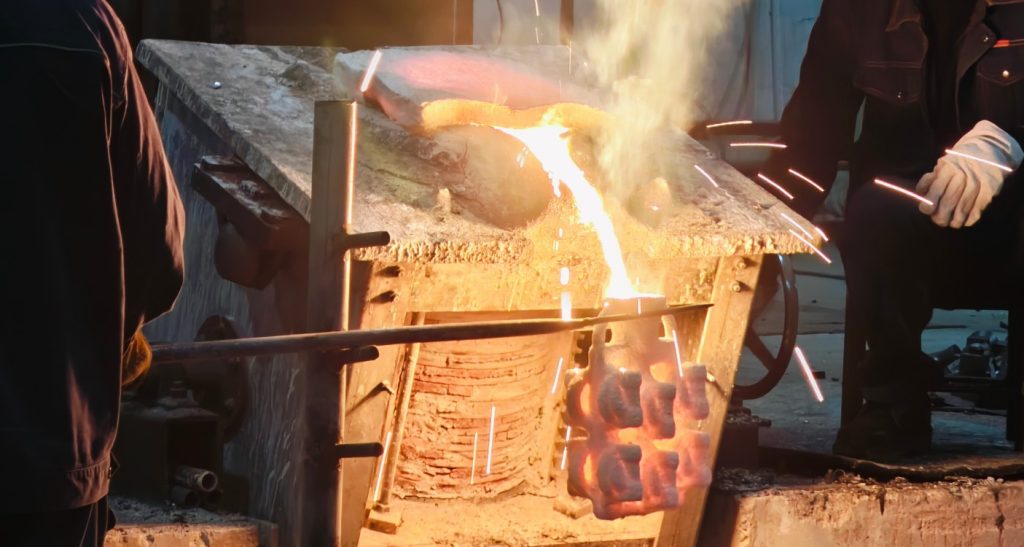
Metal smelting: Maintain precise smelting temperatures (e.g., 1600-1700℃ for stainless steel, 700-750℃ for aluminum alloy), performing deoxidation and slag removal.
Pouring temperature: Slightly above the metal liquidus temperature (e.g., stainless steel pouring temperature is 50-100℃ above melting point).
Pouring method: Use vacuum pouring or gravity pouring for defect-free metal flow.
Solidification control: Employ chills or risers for thick-walled castings to prevent shrinkage defects.
7. Post-Processing & Inspection
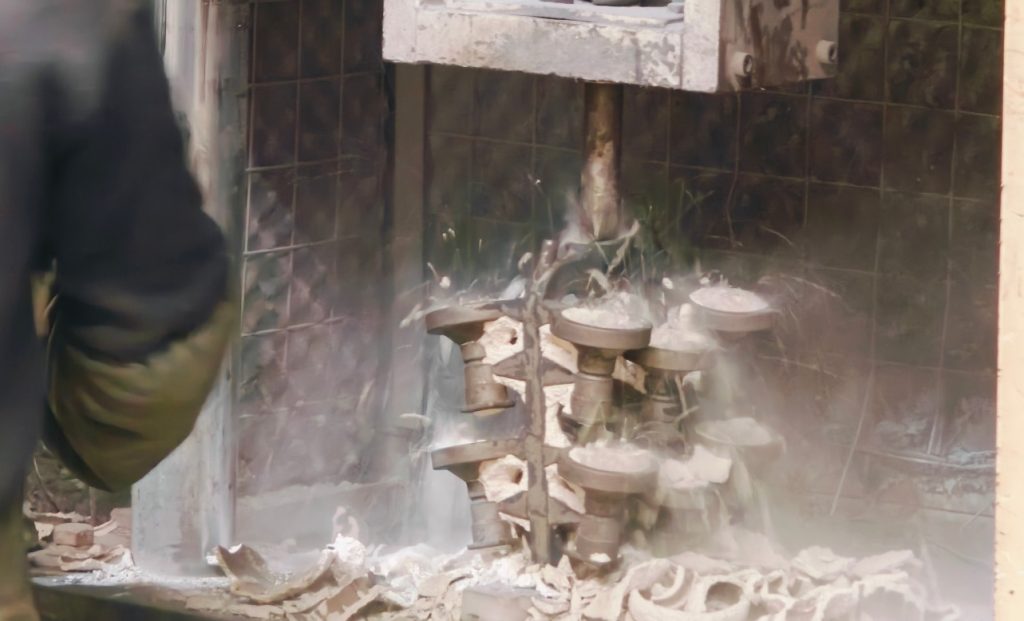
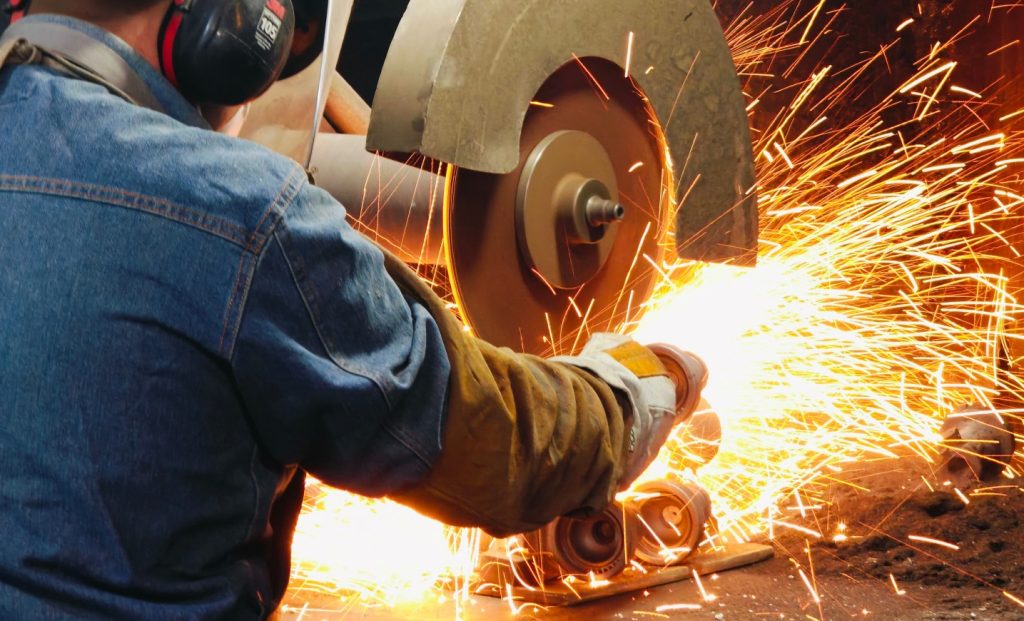
Shell removal: Use vibration or high-pressure water impact to detach the shell without damaging the casting.
Cutting: Utilize grinding wheels or wire cutting machines to remove pouring risers.
Surface treatment:
Sandblasting for a smooth finish.
Pickling (e.g., hydrofluoric acid + nitric acid for stainless steel) to enhance surface quality.
Heat treatment: Perform annealing, quenching, or aging to optimize mechanical properties.
Inspection:
Dimensional measurement: Use a CMM (Coordinate Measuring Machine) to verify precision.
Nondestructive testing (NDT): Conduct X-ray or ultrasonic testing for internal defects.
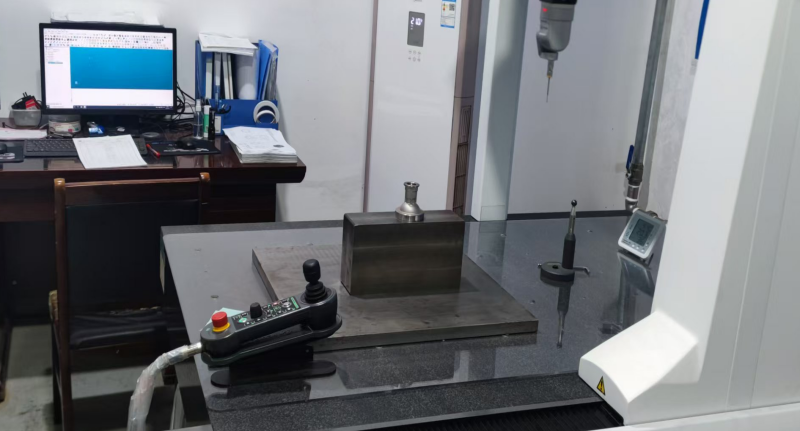
Common Defects & Solutions in Silica Sol Casting
Shell cracking: Ensure sufficient drying and control baking temperature rise.
Casting porosity: Improve shell permeability and degassing of molten metal.
Rough surfaces: Use finer sand in first layer coating and adjust slurry viscosity.
Dimensional deviation: Accurately calculate wax mold shrinkage and prevent shell deformation.
By strictly controlling process parameters (e.g., temperature, humidity, time, material ratios), silica sol casting can achieve higher yield rates and improved quality stability. Process optimization should be tailored to specific casting requirements for maximum efficiency in precision metal casting.
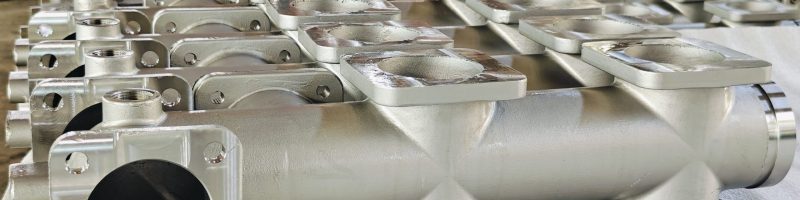
Work with us on your project
Looking for a reliable foundry partner like Tianhui Machine? Send your CAD drawings and 3D files to info@cn-tianhui.com for a quick quote!