Sand Casting
What is Sand Casting?
The sand casting process uses wet or dry sand to create a mold for casting molten metal. Most castings are produced by this ancient but novel casting process. Sand casting is one of the most popular and simplest types of casting. Sand casting can produce smaller batches than permanent mold casting, and the cost is very reasonable.
Because the sand casting process is well suited to complex geometries, it uses sand grain density, refractoriness, and recyclability to produce relatively inexpensive molds and enable rapid development and design changes at a competitive cost. For some castings of huge size and weight, the sand casting process is the first choice we should consider when choosing a suitable manufacturing method.
How Does Sand Casting Work?
The sand casting process has been finely honed over centuries. More than half of all metal castings produced worldwide are now produced this way. We have experience sand casting with a wide range of metal materials to ensure quality and craftsmanship for your next project.
- Placing: Placing the mold of the casting in the sand to ensure it takes the desired shape.
- Gating: Setting the channels that direct the molten material into the shape of the casting.
- Removal: Removing the mold pattern from the sand as the channels force the molten material into the shape you want.
- Pouring: Pouring the molten metal into the mold cavity.
- Cooling: Cooling the metal to return it from a liquid to a solid state.
- Breaking: Opening the mold to remove the newly cast metal.
Casting Service
Sand Casting Advantages
Sand casting is favored by customers who need to efficiently produce the highest quality cast metal. The process is suitable for a wide range of applications and is favored by customers and sand casting suppliers.
- Easily scalable
- Can form complex shapes
- Produce very large parts
- Reduce tooling costs
- Reduce production costs
- Shorten delivery time
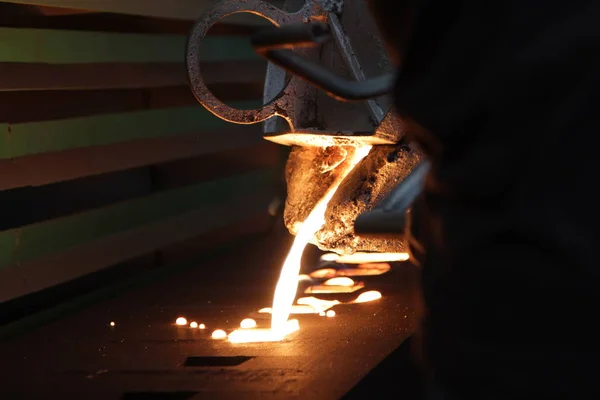
Why Choose Nbcastings for Sand Casting?
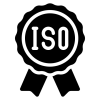
Quality Standards
Our quality standards have ISO certification, which means our components meet high standards, allowing us to optimize your costs and reduce risks.
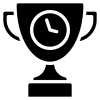
Short Lead Times
Although production of parts through investment casting tends to be lower volume and slower than other manufacturing methods, we understand that delays have a significant impact on your business. Therefore, we are committed to on-time delivery, and our lead times are among the fastest in the industry.
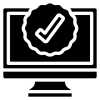
A Comprehensive Approach
The investment casting process is a start-to-finish process, starting with our design advice to ensure parts are produced to the correct standard. Throughout the project we ensure quality, consistency and streamlined supplier management.
Sand Casting Capabilities
There are many forms of sand casting, each with different costs, finishes and support weights. Nbcastings offers green sand, shell sand (resin coated sand) and hard sand casting services, giving you the opportunity to choose the type of casting that best suits your project.
Green Sand | Hard Sand | Shell Sand | |
Size Range | 0.5 – 75 kg | 45 – 10,000 kg | 0.1 – 100 kg |
Cost | Low | Low | Medium |
Design Freedom | Average | Average | Good |
Casting Soundness | Depends on design & gating | Depends on design & gating | Average |
Surface Finish | Medium | Poor | Very Good |
Development Time | 4 weeks + | 4 weeks + | 4 weeks + |
Production Time | 3 – 8 weeks | 3 – 8 weeks | 3 – 8 weeks |
Foundry Locations | Ningbo and Chizhou | Ningbo and Chizhou | Ningbo and Chizhou |
How We Test Sand Castings
Our spectrometers detect 20 chemical elements, our metallographic microscopes produce high-resolution images with 1,000x magnification, and our cleanliness meters determine particle size and count to ensure materials meet or exceed international standards. Nbcastings uses ultrasonic detectors to find defects and has an X-ray machine and accelerator that can scan castings with a maximum wall thickness of 200mm.
Nbcastings has comprehensive in-house testing capabilities including:
Spectroscopic and manual quantitative analysis
Metallographic analysis
Dimensional testing
Coordinate measuring machine
Brinell, Rockwell and Vickers hardness testing
Mechanical property analysis
Low temperature and environmental impact testing
Cleanliness testing
UT, MT and RT testing
Static and dynamic balancing
Seal and pressure testing
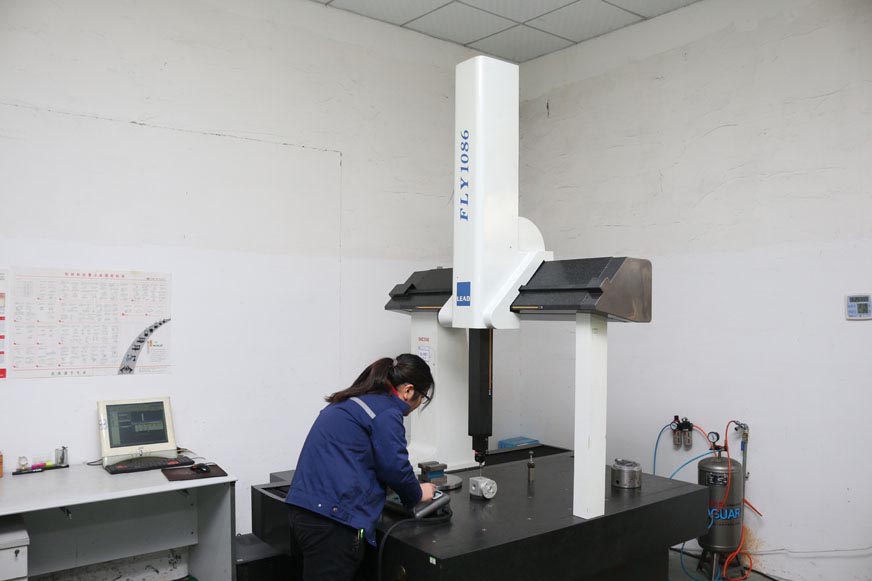
Casting Alloys Available
Sand casting services can be applied to a wide range of metals that are favored by a wide range of industries. As one of the leading sand casting companies in China, Nbcastings has the expertise to understand your project needs and recommend the best alloy for your application.
Metals | Related Market |
Stainless Steels | Martensitic, Austenitic, Duplex Marine, Pump, Valve bodies, Hydraulic components |
Carbon Steel & Low Alloy Steel | Couplings, Crankshafts, Fasteners, Bolts, Shafts, Rods, Pins |
Ductile Iron & Gray Iron | Automotive, Pipe Fittings, Valves, Hydraulic Components, Bearings |
Bronzes | Bearings, Gears, Sliding Components, Pump Impellers, Valve Bodies, Architecture |
Industries We Serve
Nbcastings is proud to provide high quality sand casting services to businesses across a wide range of industries. We understand the importance of reliable castings that will not exhibit any defects during use.
Nbcastings produces near net shape, high quality, durable investment castings for pumps and valves.
Agricultural applications often require looser tolerances, and investment castings have been a major market for this industry for decades.
Our role in automotive precision casting is primarily focused on the aftermarket, or replacement parts that are not produced by the original manufacturer (OEM).
Nbcastings has been producing quality investment castings for companies in the medical industry.
Investment castings used in the oil and gas industry require the highest quality, durability, and corrosion resistance.
Nbcastings has the capabilities and technical expertise to meet the needs of the food processing industry.
Have Questions Left Unanswered?
Nbcastings has many years of expertise in the casting field and can support your project from start to finish. Our team of experts can help you with everything from selecting the right alloy to ensuring the most efficient casting process to meet your specific needs.