Nickel Alloys Casting
Nickel Alloys Casting
Nickel alloys are known for their unique combination of corrosion resistance, high temperature performance and mechanical properties. These alloys are well suited for challenging environments where traditional materials may fail. Nickel alloys are the first choice for critical applications across a wide range of industries that require reliability, durability and performance under extreme conditions.
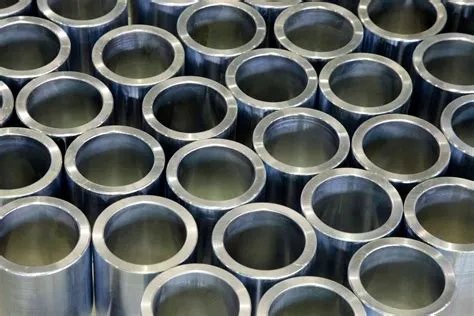
Main Characteristics of Nickel Alloys Casting
Nickel alloys offer excellent resistance to a wide range of corrosive chemicals, including acids, chlorides, and sulfides.
These alloys retain their mechanical properties at elevated temperatures, making them suitable for high-temperature applications and thermal cycling.
Some nickel alloys exhibit low magnetic permeability, making them ideal for applications where magnetic interference must be minimized.
Select nickel alloys have good resistance to creep deformation and excellent resistance to high-temperature oxidation.
When to Use Nickel-based Alloy Casting
As a high-end manufacturing technology, the timing of nickel-based alloy casting directly affects product performance and economic value. Under specific working conditions, choosing nickel-based alloy casting can significantly improve equipment performance, extend service life, and bring considerable economic benefits. This choice is based on a comprehensive consideration of the use environment, performance requirements and cost-effectiveness.
1. High-temperature environment application
In the field of aerospace, nickel-based alloy casting is an irreplaceable choice. The operating temperature of engine turbine blades exceeds 1000℃, and nickel-based alloy casting must be used to ensure performance. After a certain model of aircraft engine uses nickel-based alloy casting blades, the thrust is increased by 15% and the service life is extended by 30%.
Energy equipment manufacturing is another important application field of nickel-based alloy casting. In supercritical generator sets, nickel-based alloy castings can withstand operating temperatures above 650℃. After a power plant uses nickel-based alloy casting components, the power generation efficiency is increased by 5%, and the annual coal cost savings exceed 10 million yuan.
High-temperature reactors in the petrochemical industry also widely use nickel-based alloy casting. After a petrochemical enterprise adopted nickel-based alloy casting reactor, the service life of the equipment was extended from 5 years to 20 years, saving 5 million yuan in equipment replacement costs annually.
2. Application in corrosive environment
In the field of marine engineering, nickel-based alloy casting shows excellent corrosion resistance. The key components of deep-sea drilling platforms are cast with nickel-based alloys, which can work stably for more than 20 years in a deep-sea environment of 3,000 meters. After a certain offshore oil field adopted nickel-based alloy castings, the annual maintenance cost was reduced by 40%.
In the manufacture of chemical equipment, nickel-based alloy casting solves the problem of strong corrosive media. After a sulfuric acid production enterprise adopted nickel-based alloy casting equipment, the service life of the equipment was extended to 15 years, saving 2 million yuan in maintenance costs annually.
In the construction of nuclear power plants, nickel-based alloy casting ensures the long-term and stable operation of equipment. After a nuclear power plant adopted nickel-based alloy casting steam generator tube sheets, the design life of the equipment was extended to 60 years, and the annual power generation increased by 15%.
3. Special performance requirements
In situations where excellent mechanical properties are required, nickel-based alloy casting is an ideal choice. After a heavy-duty gas turbine used nickel-based alloy to cast the rotor, the output power increased by 20%, and the annual power generation income increased by 30 million yuan.
For complex-shaped parts, nickel-based alloy casting can achieve precision molding. After a certain aviation company used nickel-based alloy to cast complex structural parts, the number of parts was reduced by 50% and the assembly efficiency was increased by 40%.
In occasions where special physical properties are required, nickel-based alloy casting provides solutions. After a high-temperature sensor used nickel-based alloy to cast the shell, the measurement accuracy increased by 30% and the service life was extended by 3 times.
The timing of the application of nickel-based alloy casting reflects the extreme pursuit of material performance in modern industry. In extreme environments such as high temperature and corrosion, nickel-based alloy casting shows irreplaceable advantages.
Industries We Serve
Nbcastings is the trusted casting supplier of businesses across a wide variety of industries. Our precise metal casting moulds and supply of high-quality materials mean we are the ideal partner for projects that require intricate products, engineered to tight tolerances.
Nbcastings produces near net shape, high quality, durable investment castings for pumps and valves.
Agricultural applications often require looser tolerances, and investment castings have been a major market for this industry for decades.
Our role in automotive precision casting is primarily focused on the aftermarket, or replacement parts that are not produced by the original manufacturer (OEM).
Nbcastings has been producing quality investment castings for companies in the medical industry.
Investment castings used in the oil and gas industry require the highest quality, durability, and corrosion resistance.
Nbcastings has the capabilities and technical expertise to meet the needs of the food processing industry.
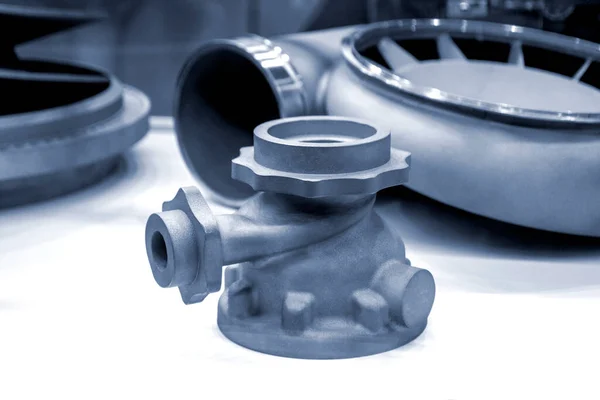
Excellent investment casting nickel alloy parts solutions
Speak to one of our experts today to learn more about our custom casting solutions.