Investment casting (lost wax casting) is a high-precision casting process that is suitable for a variety of materials, especially for complex shapes and thin-walled parts. The choice of different materials depends on their performance requirements, application scenarios and cost factors. As an excellent investment casting manufacturer in the foundry industry, Tianhui Machine is pleased to provide this comprehensive guide to guide you on how to choose the right material for your investment casting project.
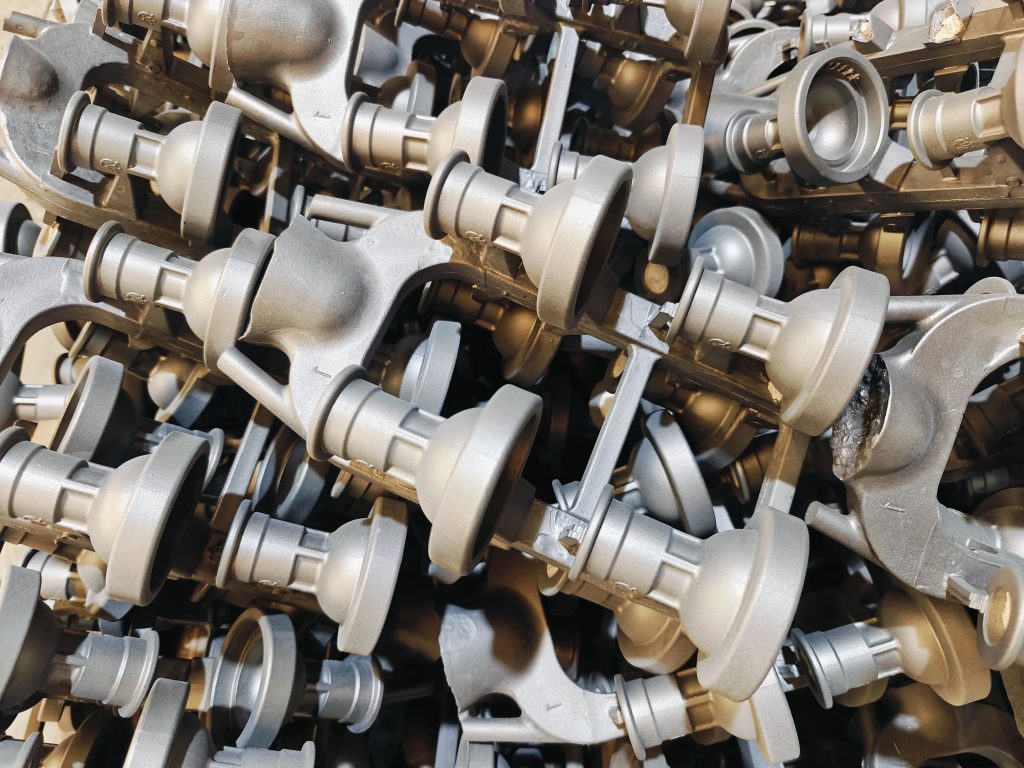
Why Material Selection Matters
The investment casting material you choose can significantly affect the physical properties of your part, including its strength, hardness, corrosion resistance, and heat resistance. These properties will affect how the part performs in its end-use environment. Therefore, it is critical to understand the specific requirements of your application before selecting a casting material.
Different Materials for Investment Casting
At Tianhui Machine, we offer a wide variety of investment casting materials to meet a variety of industry needs. The following are common investment casting materials:
1. Stainless steel
Common grades: 304, 316, 17-4PH, 2205 duplex steel, etc.
Features:
Corrosion resistance: Suitable for corrosive environments such as chemical, marine, and medical.
Strength: High mechanical strength and high temperature resistance (such as 17-4PH).
Processability: Investment casting can avoid deformation problems in traditional processing.
Applications:
Medical devices (surgical tools, implants).
Chemical valves, pump bodies.
Food processing equipment components.
2. Aluminum alloy
Common grades: A356, ZL101, AlSi7Mg.
Features:
Lightweight: low density, suitable for scenes with high weight reduction requirements.
Thermal conductivity: excellent heat dissipation performance (such as electronic device housing).
Low cost: material and processing costs are lower than titanium alloys and high-temperature alloys.
Applications:
Automobile engine parts (pistons, cylinder heads).
Aerospace lightweight parts.
Electronic equipment radiators.
3. Copper alloys
Common types: bronze (such as C93200), brass (such as C36000), beryllium copper (C17200).
Features:
Electrical/thermal conductivity: suitable for electrical components and radiators.
Wear resistance: bronze is often used for bearings and gears.
Corrosion resistance: brass performs well in freshwater environments.
Applications:
Marine accessories (propellers, valves).
Electrical connectors, switch parts.
Artwork casting (complex textures).
How to Choose the Right Investment Casting Material?
Choosing the right investment casting material is a critical step that directly affects part performance, cost, and production efficiency. The following are the main factors to consider when choosing investment casting materials:
1. Working environment of parts
Temperature:
High temperature environment (such as aircraft engines, gas turbines) → Select high temperature alloys (such as nickel-based alloys, cobalt-based alloys).
Normal or medium temperature environment → Stainless steel, aluminum alloy, copper alloy.
Corrosiveness:
Strong corrosive environment (such as chemical industry, ocean) → Select corrosion-resistant materials (such as 316 stainless steel, titanium alloy).
Weakly corrosive or non-corrosive environment → Ordinary stainless steel, aluminum alloy.
Wear and impact:
High wear environment (such as molds, bearings) → Select tool steel, bronze.
High impact environment → Select high toughness materials (such as titanium alloy, high-strength stainless steel).
2. Parts performance requirements
Strength and hardness:
High strength requirements → Choose titanium alloy, high temperature alloy, high strength stainless steel (such as 17-4PH).
High hardness requirements → Choose tool steel (such as H13, D2).
Lightweight:
High lightweight requirements → Choose aluminum alloy, magnesium alloy, titanium alloy.
Electrical conductivity/thermal conductivity:
High electrical conductivity/thermal conductivity requirements → Choose copper alloy, aluminum alloy.
3. Cost factors
Material cost:
Precious metals (gold, silver, platinum) and titanium alloys are more expensive and suitable for high value-added products.
Aluminum alloys, copper alloys, and ordinary stainless steel are less expensive and suitable for mass production.
Processing cost:
High-temperature alloys and titanium alloys are difficult to process and have higher costs.
Aluminum alloys and copper alloys are relatively simple to process and have lower costs.
4. Shape and size of parts
Complex shapes:
Investment casting is suitable for complex shapes, but some materials (such as high-temperature alloys) may produce defects under complex shapes.
Thin-walled parts:
Aluminum alloys and magnesium alloys are suitable for thin-walled parts and have good fluidity.
High-temperature alloys and titanium alloys require strict process control in thin-wall casting.
5. Subsequent processing requirements
Processability:
Aluminum alloys and copper alloys have good processing performance and are suitable for parts that require subsequent processing.
High-temperature alloys and titanium alloys are difficult to process and have high costs.
Heat treatment:
Some materials (such as stainless steel and titanium alloys) require heat treatment to improve performance, and the cost of heat treatment needs to be considered.
Material Selection Examples
Application Scenario | Recommended Material | Selection Reason |
---|---|---|
Aircraft Engine Turbine Blades | Nickel-based Superalloys (e.g., Inconel 718) | High temperature resistance, oxidation resistance, and creep resistance. |
Medical Implants | Titanium Alloys (e.g., Ti-6Al-4V) | Biocompatibility, high strength, and corrosion resistance. |
Automotive Engine Components | Aluminum Alloys (e.g., A356) | Lightweight, good thermal conductivity, and low cost. |
Chemical Valves | Stainless Steel (e.g., 316L) | Corrosion resistance and high strength. |
Electronic Heat Sinks | Copper Alloys (e.g., C17200 Beryllium Copper) | High thermal and electrical conductivity. |
Jewelry | Precious Metals (Gold, Silver, Platinum) | High ductility, oxidation resistance, and aesthetic appeal. |
Tianhui Machine: Your material selection partner
At Tianhui Machine, we are dedicated to helping our customers select the best materials for their investment casting projects. We understand that every project is unique, and our team of experts is ready to provide personalized advice based on your specific needs and requirements.
Selecting the right investment casting material is not something to be taken lightly. It is a critical choice that can impact the success and efficiency of your project. Let us guide you through this process to ensure the best possible results for your investment casting project.
If you are ready to start your next investment casting project or have any questions about material selection, please feel free to contact Tianhui Machine. Your success is our mission, and we are eager to help you achieve it.
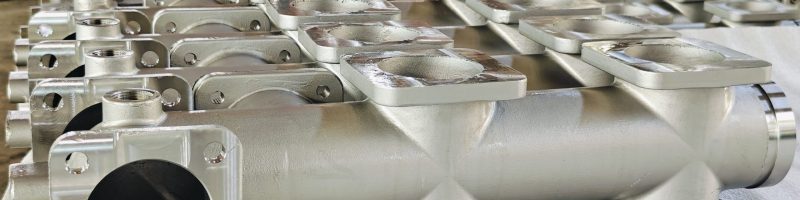
Work with us on your project
Looking for a reliable foundry partner like Tianhui Machine? Send your CAD drawings and 3D files to info@cn-tianhui.com for a quick quote!