Turbine Flange Ball Valve
Material: Stainless steel 304/316
Process: Customized process, fine processing according to drawings
Process type: Silica sol precision casting
Machining surface roughness: Ra0.8-1.6
Inspection report: Material report, dimensional inspection report, heat treatment report, etc. can be provided
Product Details
Product Overview
Turbine Flange Ball Valve, using silica sol precision casting process to make casting blanks, material CF8 or CF8M, through CNC precision machining to remove the excess, so that the workpiece size within the tolerance range required by the drawing, to ensure that it is suitable for product use and assembly. Stainless steel precision casting products are widely used in industry, construction, pipelines and other industries.
Technical Parameters
Category | Details |
---|---|
Process | Silica sol precision casting + precision machining |
Material | Stainless steel |
Material Standards | ASTM/AISI 304, AISI 316, DIN 1.4308, DIN 1.4408, JIS SCS13, SCS14 |
Casting Weight | 0.5KG – 150KG |
Casting Dimensional Tolerance | CT5-CT6 level |
Casting Surface Roughness | Ra 3.2 – 6.4 |
Machining Surface Roughness | Ra 0.8 – 1.6 |
Supported Drawing File Formats | ProE (.igs, .stp), AutoCAD, PDF, JPEG, JPG, PNG |
Product Process Documents | Product casting process card, machining process card, product inspection card |
Heat Treatment | Solution heat treatment (1050°C, holding for 2 hours or more) |
Machining Equipment | 50 CNC machines, 800 vertical machining center |
Inspection | Three inspections: first inspection, in-process inspection, final inspection |
Measuring Tools | CMM, projector, pneumatic gauge, micrometer, internal diameter gauge |
Inspection Method | Three inspections: first inspection, in-process inspection, final inspection |
Available Reports | Casting material report, product dimensional inspection report |
Casting Capacity
We only produce high-quality precision castings. First, the object to be cast is replicated with wax, then immersed in a pool containing ceramic and left to dry, so that the wax replica is covered with a layer of ceramic outer film, and the steps are repeated until the outer film is sufficient to support the casting process (about 1/4 inch to 1/8 inch), then the wax in the mold is melted and the mold is pulled out. After that, the mold needs to be heated several times to enhance the hardness before it can be used for casting. The castings are sharp and angular, with precise dimensions (critical dimensions can reach ct5-ct6 level) and smooth surfaces (casting surface roughness Ra 6). Castings can also be shaped, and presses, fixtures and gauges can be used to correct castings.
Before the raw materials are put into storage, they are subjected to spectral analysis + mechanical property testing, three-dimensional coordinate measurement (CMM) + industrial CT scanning, 100% full-size report delivery, and the roughness of key sealing surfaces Ra≤0.8μm. Through IATF 16949/AS9100D certification, a full-process MES traceability system is established. Each part can query the production batch and process parameters with one click, helping customers to quickly respond to terminal problems, providing one-stop services from blank casting to finishing, reducing customer management costs, and the value of precision manufacturing is not only to meet standards, but also to exceed expectations. If you need a pump and valve parts solution that takes into account reliability, cost and delivery, we look forward to supporting you with 20 years of industry experience.
Our Process
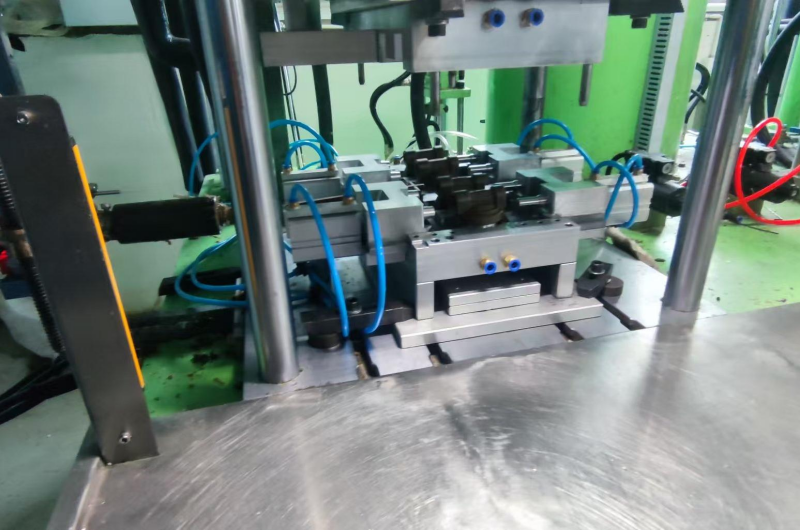
1.Wax Making
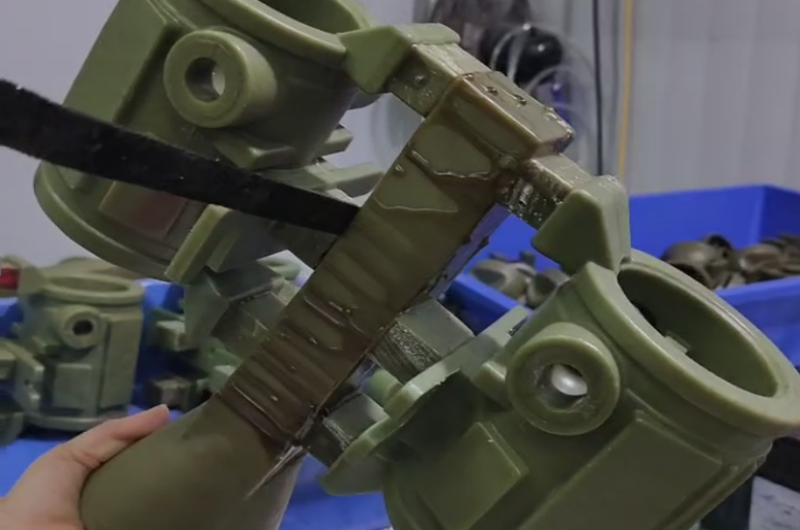
2.Wax Assembly
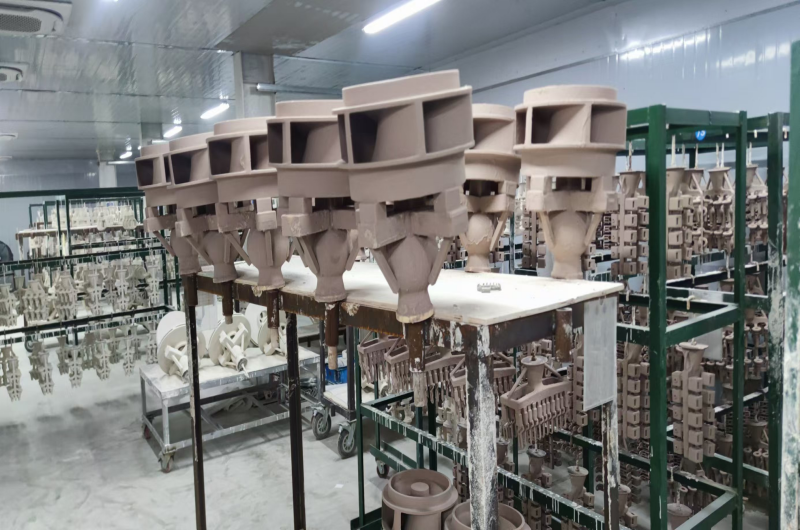
3.Shell Making
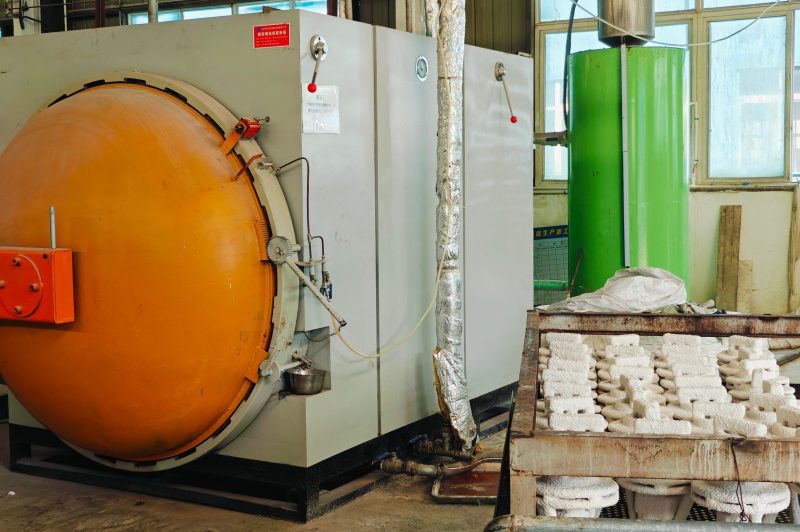
4.Dewaxing
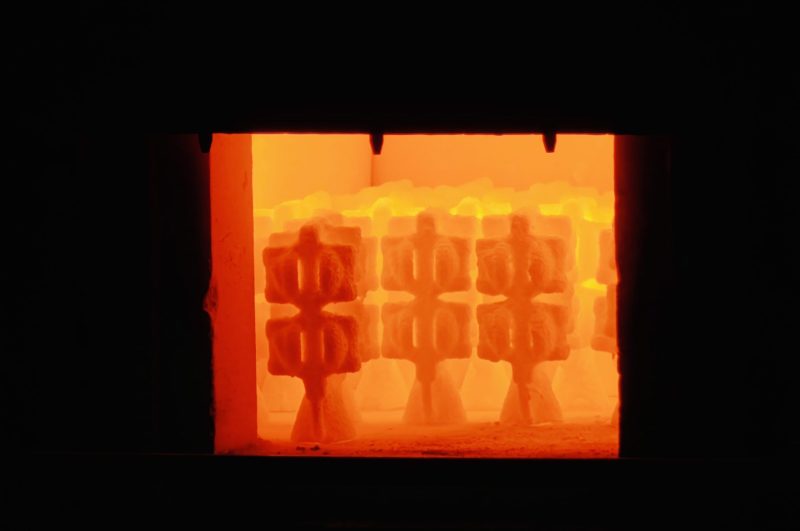
5.Shell Firing
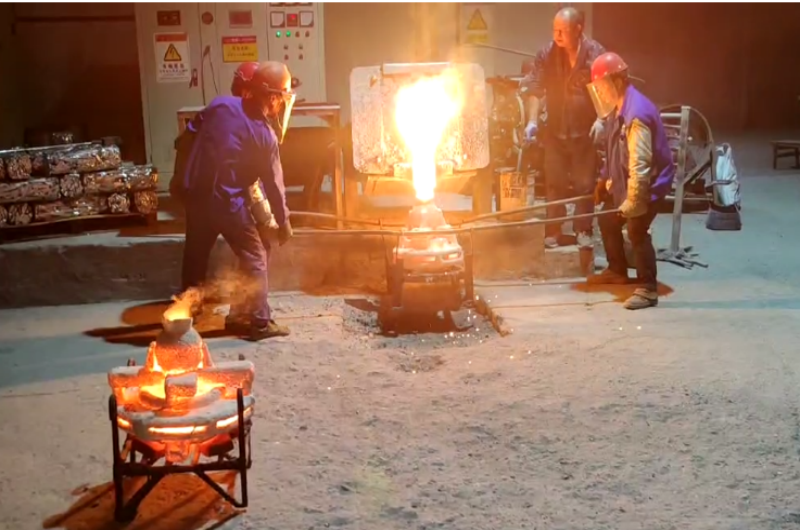
6.Pouring

7.Knock Out
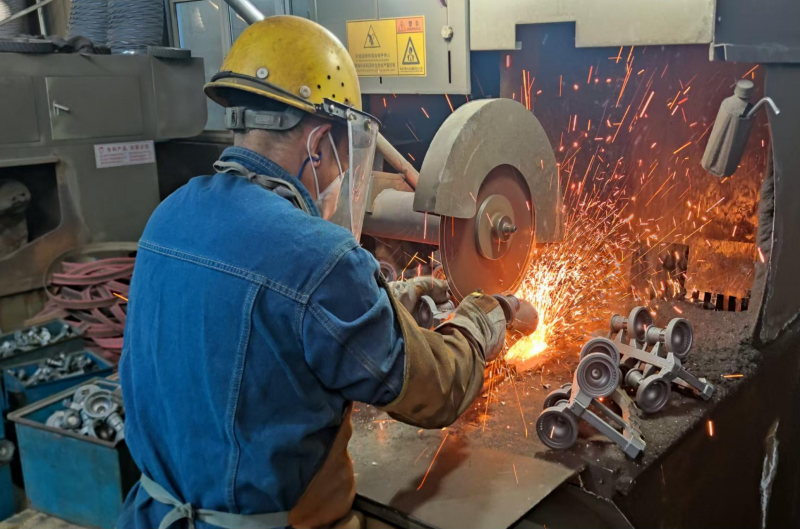
8.Cut Off
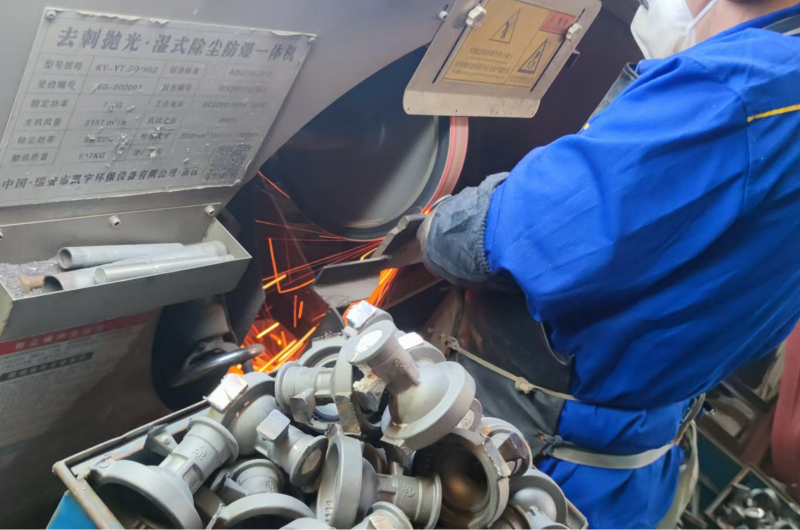
9.Finishing
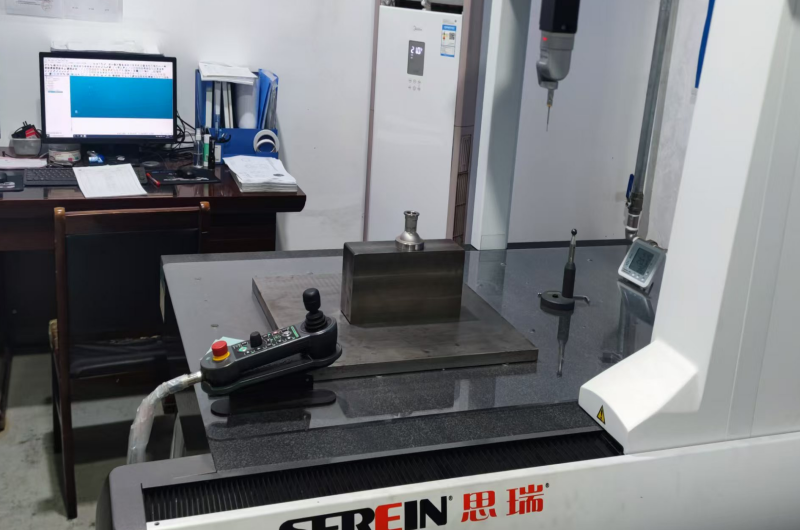
10.Inspection
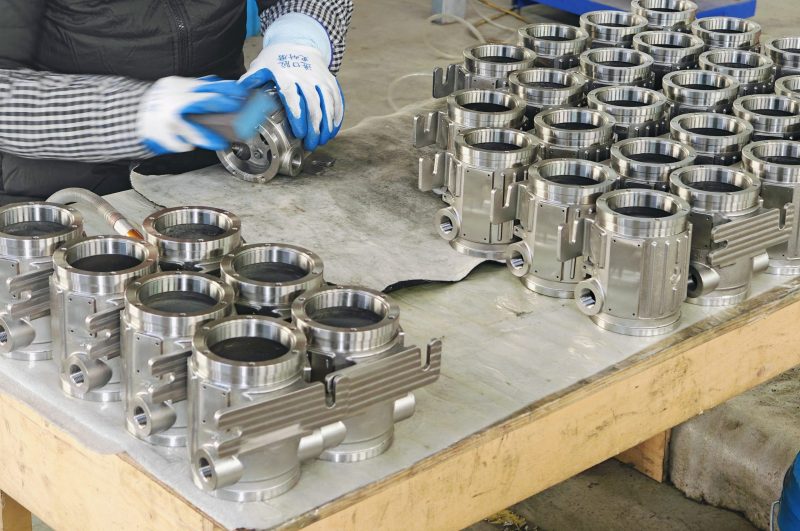
11.Check and Wipe
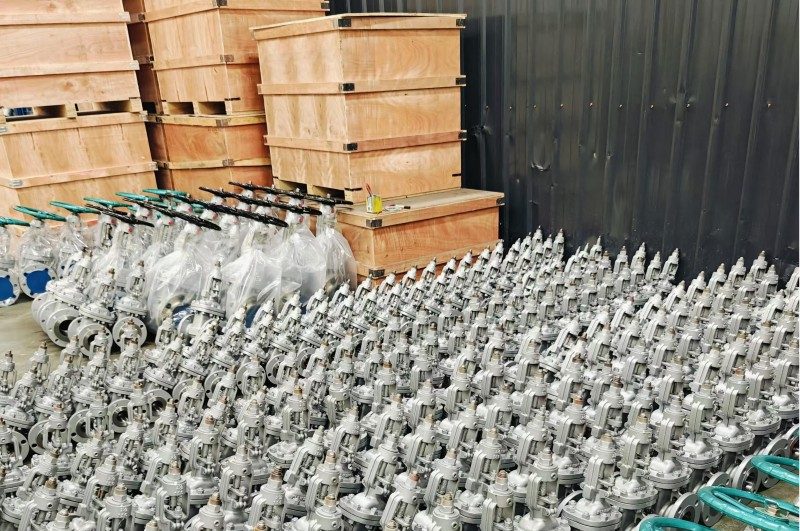
12.Shipping Packaging
Machining production and inspection capabilities
Quotation, order acceptance, and production control
We receive customer inquiry drawings. We will carefully analyze the processing dimensions and technical requirements for each drawing, check the relevant standards, and quote the best price. Before accepting an order, we will review the relevant production process and enter it into the ERP system. From raw material procurement to blank delivery, each process is controllable. If necessary, we can make PPAP and other process control plans. Intermediate processing and production are produced according to the production process card and the flow order, and comply with the first inspection of the first piece in production, morning inspection and random inspection (self-inspection by operators) during production. Final inspection before shipment to ensure product quality. Customize packaging consumables according to the customer’s packing and shipping requirements during shipment to ensure logistics and transportation safety.
Test Report
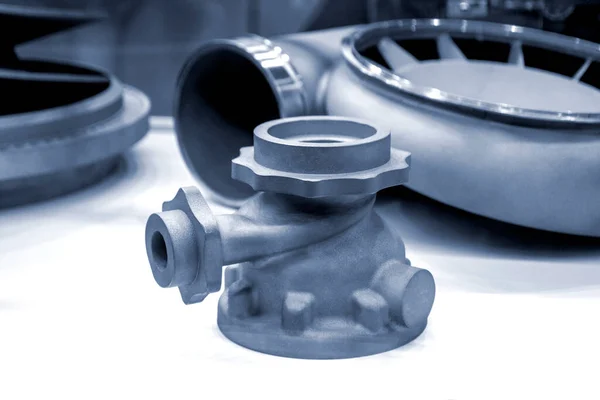
Excellent investment casting pump and valve parts solutions
Speak to one of our experts today to learn more about our custom casting solutions.