Modern Industrial Applications of Four Types of Corrosion-resistant Metal Castings
Casting technology is one of the oldest metal processing technologies of mankind. It has continued from the Bronze Age to the present day and still plays an important role in modern industry. Stainless steel castings, nickel-based alloy castings, aluminum castings and copper castings, these four metal castings with excellent corrosion resistance, are writing a new chapter in modern casting technology. With their unique performance advantages, they shine in key fields such as aerospace, energy equipment, and transportation, and promote modern industry to develop in a higher, more refined and stronger direction.
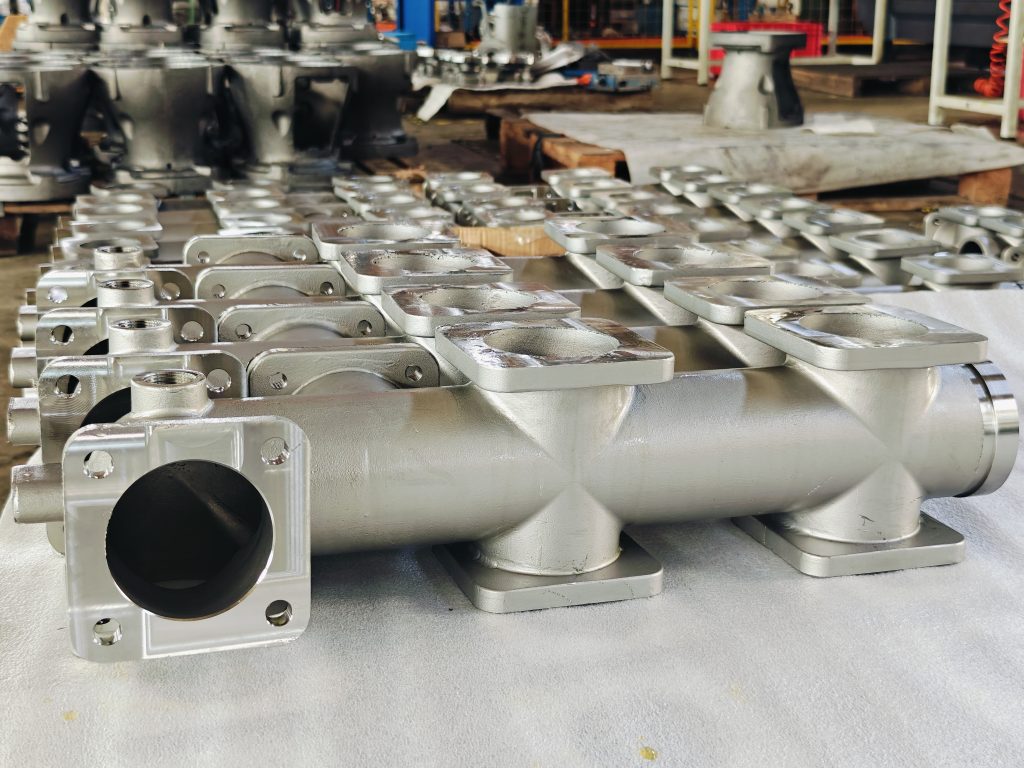
Stainless steel castings occupy an important position in the field of chemical equipment manufacturing. Key components such as large reactors and pump and valve housings are cast in stainless steel, which can withstand corrosion from strong acids and alkalis. After a chemical company adopted stainless steel castings, the service life of the equipment was extended from 3 years to 15 years, saving more than 20 million yuan in annual maintenance costs.
In the field of food machinery, the hygienic properties of stainless steel castings are fully reflected. From food delivery pumps to mixing containers, stainless steel castings ensure food safety and hygiene. More than 90% of the world’s food processing equipment uses stainless steel castings, with an annual output value of more than 50 billion US dollars.
Architectural decoration is another important application direction of stainless steel castings. From door handles to artistic sculptures, stainless steel castings show unique artistic charm. A landmark building is decorated with stainless steel castings. After 20 years of wind and rain, it is still as bright as new and has become a symbol of urban culture.
In the field of aerospace, nickel-based alloy castings show their excellent performance. The engine turbine blades use precision casting technology and can withstand high temperatures of more than 1000°C. In modern aircraft engines, nickel-based alloy castings account for more than 50% and are key components to ensure flight safety.
Energy equipment manufacturing is another important application direction of nickel-based alloy castings. In nuclear power plants, nickel-based alloy castings are used to manufacture key components such as steam generator tube sheets. After a nuclear power plant uses nickel-based alloy castings, the service life of the equipment is extended to 60 years, and the annual power generation is increased by 15%.
In the field of marine engineering, the seawater corrosion resistance of nickel-based alloy castings is fully utilized. The key components of deep-sea drilling platforms are cast with nickel-based alloys, which can work stably for more than 20 years in a deep-sea environment of 3,000 meters. After a certain offshore oil field uses nickel-based alloy castings, the annual maintenance cost is reduced by 30%.
The application of aluminum alloy castings in the automotive industry has promoted the lightweight revolution. From the engine block to the gearbox housing, aluminum castings significantly reduce the weight of the vehicle body. After a certain new energy vehicle uses aluminum castings, the cruising range is increased by 20%, and the annual carbon emissions are reduced by about 1.5 tons.
In the field of electronic products, aluminum casting radiators ensure the stable operation of equipment. From smartphones to 5G base stations, aluminum casting radiators play a key role. After a certain brand of laptops adopts a new aluminum casting cooling system, the CPU temperature is reduced by 15°C and the performance is improved by 20%.
Aerospace is another important application direction of aluminum castings. Aircraft structural parts are cast with high-strength aluminum alloys, which reduce weight while ensuring strength. After a certain type of passenger aircraft uses aluminum castings, the fuel efficiency is increased by 10%, and the annual fuel cost savings exceed 10 million US dollars.
4. Copper castings
Copper castings show eternal charm in the field of art. From bronze sculptures to architectural decorations, copper castings carry the memory of human civilization. The bronze statues in Florence, Italy have gone through hundreds of years of wind and rain and are still radiant, witnessing the artistic value of copper castings.
In the electrical industry, copper castings play an important role. From high-voltage switches to motor housings, copper castings ensure the reliable operation of power equipment. More than 60% of the copper castings produced annually in the world are used in the electrical industry, supporting the operation of modern power systems.
Building water supply and drainage systems are another important application area for copper castings. Copper casting pipes and valves ensure water safety and have a service life of more than 50 years. After a large hospital adopted a copper casting water supply system, the water quality qualified rate increased to 99.9%.
Conclusion
As a professional metal casting manufacturer, Tianhui Machinery Foundry is familiar with the characteristics of each casting metal and has rich experience in casting technology. According to your design and application, we can recommend the most suitable metal casting materials and provide customers with the best quality castings.
If your project requires casting high corrosion-resistant metals, please contact us immediately and send us the drawings by email. We will get back to you as soon as possible!