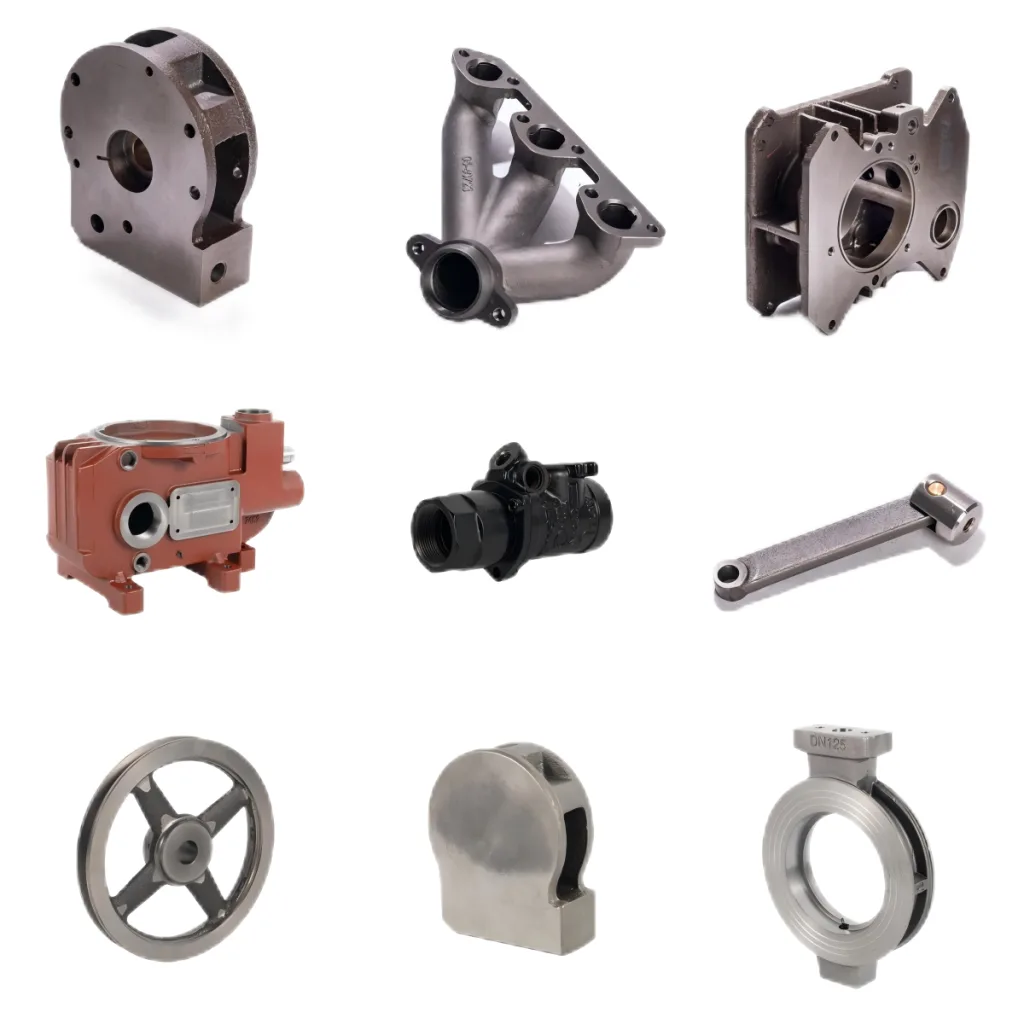
Sand Casting Parts
Sand casting is favoured by customers who need an efficient method of producing cast metals of the highest quality. Suitable for a wide range of applications, the process is favoured by customers and sand casting suppliers alike.
- Easy to scale
- Complex shapes can be formed
- Produce very large parts
- Lower cost for tooling
- Lower production costs
- Have a shorter lead time
What products are made from sand casting?
Sand casting is ideal for large part production compared to other casting methods. This method provides engineers with a wide range of metal alloy options and part size options, and it is inexpensive to manufacture. Additionally, sand casting has low setup costs and low mold modification costs. It is the preferred casting method in the aerospace industry, and other industries such as construction, automotive, manufacturing, and even the marine industry also use sand casting.
Common Products & Use Cases of Sand Casting
- Engine blocks
- Pipes
- Nuts
- Landing gear
- Pulleys
- Cylinder heads
- Aerospace components
- Machine tool bases
Comparison between sand casting and investment casting
Both methods have been around for centuries, but the end product will determine which is best.
Sand Casting Services
- A range of different parts or several of the same part may share a mold.
- New molds are easy to remake.
- Higher casting weight limit.
- Greater ease of changing design.
- Difficult to cast parts with internal voids.
Investment Casting Services
- Ceramic mold (initial investment) is destroyed to get parts.
- Better equipped to make small, intricate parts.
- More complex and labor-intensive.
- Hundreds of small parts can be cast at once.
- Excellent surface finish.
- Greater design freedom.
Frequently Asked Questions
Why is Sand Casting Used?
Sand casting is widely used because of its ability to cast metals that have high melting temperatures, low cost, and flexible production options. Unlike other casting options, sand casting is an affordable way to cast larger parts without expensive machining costs.
What is The Difference Between Sand Casting and Investment Casting?
Both sand casting and investment casting have been around for many years. Investment casting is often used when an engineer or designer needs a smaller part with intricate details. Sand casting can produce larger, heavier parts at a lower cost. Investment casting tends to be more labor-intensive because mold making requires more steps before casting and additional machining steps after the metal cools.
Is Sand Casting Expensive?
Out of the most widely used metal casting methods, sand casting is the least expensive for smaller batch runs. It is also a cost-effective model for large part production
What Types of Sand are Used to Produce Molds for Sand Casting?
The three types of sand used for sand casting are green sand, silica sand, and resin sand. Casting with green sand is quick and cheap because the sand can be reused for subsequent castings. Its soft, reusable nature also means that the mold can shift or collapse during the casting process. Silica sand is a good choice because it changes from liquid to solid quickly. Casting with silica sand takes more time because an extra step is required to break down the mold after the metal cools. Resin sand gives the mold a smooth surface, which means fewer defective parts. This type of sand also has slower casting times and is more expensive.