Stainless steel investment casting and CNC machining: the perfect combination of precision manufacturing
In modern manufacturing, stainless steel is widely used in aerospace, automotive, medical, food processing and industrial equipment due to its excellent corrosion resistance, strength and beautiful appearance. When manufacturing high-precision complex parts, the combination of stainless steel investment casting and CNC machining has become an ideal solution. This article will explore the characteristics and advantages of these two processes and how to optimize the combination of the two to improve product quality and production efficiency.
Stainless steel investment casting: an ideal choice for high-precision and complex structures
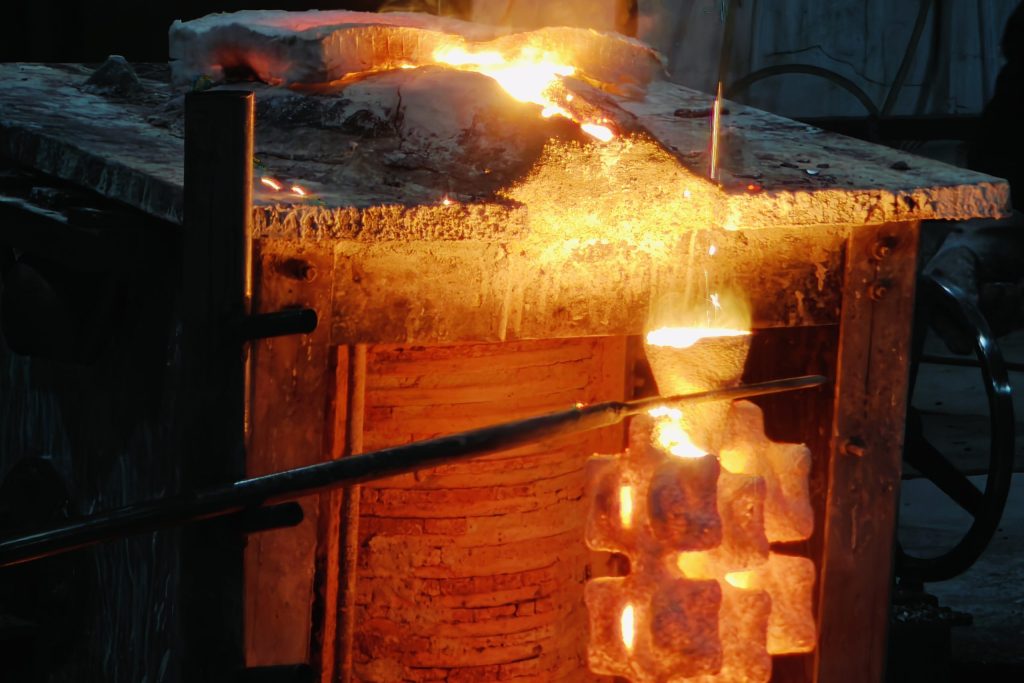
1. What is investment casting?
Investment casting, also known as precision casting or lost wax casting, is a casting process that can manufacture complex shapes and high-precision parts. Its basic principles are:
Wax mold manufacturing: wax is used to make a wax mold with the same shape as the final part.
Shell mold preparation: the wax mold is immersed in a refractory ceramic slurry, sprinkled with refractory sand, and dried and repeated many times to form a solid ceramic shell.
Dewaxing and sintering: Heat the wax mold to melt the wax and flow out, then sinter the ceramic shell at high temperature to increase its strength.
Melting and pouring: Melt the stainless steel and pour it into the shell mold, wait for it to cool and solidify to form a casting.
Cleaning and finishing: Remove the ceramic shell, cut the runner, surface treat, and perform necessary heat treatment to improve the material properties.
2. Advantages of stainless steel investment casting
✅ High precision and complex shapes: Investment casting can produce parts with uniform wall thickness and fine details, avoiding the limitations of traditional casting.
✅ Excellent surface quality: The surface of the casting is smooth, reducing the need for subsequent processing and improving the yield rate.
✅ High material utilization: Reduces waste generated by mechanical processing, making the manufacturing process more environmentally friendly.
✅ Applicable to a variety of stainless steel alloys: including 304, 316, 17-4PH, etc., to meet different application requirements.
3. Applicable scenarios
Investment casting is widely used in the manufacture of pump and valve components, aerospace parts, medical equipment, food machinery parts, precision instrument housings and other high-demand fields.
CNC machining: improving precision and functionality
Although investment casting has high precision, CNC machining is still required to further improve dimensional accuracy and functionality within certain extremely high tolerance ranges.
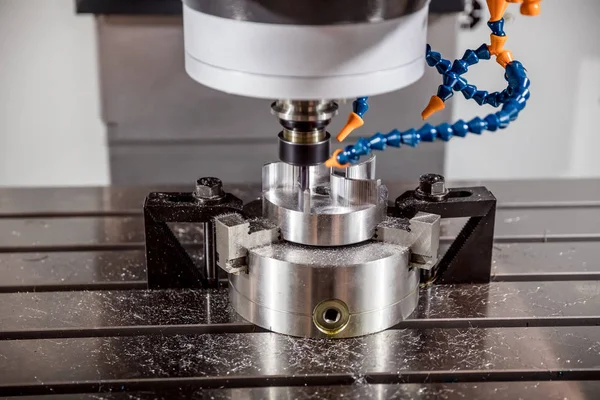
1. Main processes of CNC machining
CNC turning: suitable for cylindrical parts, can efficiently remove excess material and achieve precision machining.
CNC milling: used for machining planes, grooves, holes, etc., suitable for parts with complex geometries.
Drilling and tapping: perform additional hole machining or thread machining on castings to meet assembly requirements.
2. Challenges and solutions for stainless steel CNC machining
🔹 Challenge 1: High material hardness and easy wear of tools
✅ Solution: Use high-hardness tools (such as carbide tools) and reasonably select cutting speed and feed rate.
🔹 Challenge 2: Stainless steel is prone to work hardening
✅ Solution: Use slower cutting speeds and greater cutting depths to avoid repeated cutting of machined surfaces.
🔹 Challenge 3: Poor thermal conductivity, which can easily lead to tool overheating
✅ Solution: Use coolant (emulsion or oil-based coolant) to reduce cutting temperature and improve machining efficiency.
3. The role of CNC machining in investment casting
Correct casting tolerances and improve precision
Add additional mechanical features such as threaded holes and fine slots
Improve surface quality and remove casting residues
Ensure that parts meet final assembly requirements
Investment casting + CNC machining: Application cases of perfect combination
Case 1: High-end medical device parts
The medical industry has extremely high requirements for part precision, surface finish and material cleanliness. For example, surgical tools and implantable medical devices usually use 316L stainless steel, which is formed into a basic shape through investment casting, and then refined through CNC machining to achieve ultra-high precision.
Case 2: Aerospace turbine blades
The turbine blades of aircraft engines require extremely high heat resistance and structural complexity. Usually, the initial shape is manufactured by investment casting, and the curved shape of the blade is refined by CNC machining to improve aerodynamic performance.
Case 3: High-performance automotive parts
For example, turbocharger housings, stainless steel exhaust manifolds, etc., complex geometric shapes are manufactured by investment casting, and then the mounting holes and sealing surfaces are adjusted by CNC machining to improve assembly accuracy and durability.
How to optimize the combination of investment casting and CNC machining?
1. Optimization in the design stage
Fully consider the tolerance requirements of casting and machining during CAD design to avoid unnecessary over-machining.
Adopt the DFM (Design for Manufacturing) concept to optimize the shape of parts and reduce difficult-to-process areas.
2. Choose the right stainless steel material
304/316L: Strong corrosion resistance, suitable for food, medical, and chemical equipment.
17-4PH: High strength and wear resistance, suitable for aerospace and machinery manufacturing.
3. Use efficient tools and processing parameters
Choose appropriate tool materials (such as coated carbide) to improve cutting efficiency.
Use optimized feed speed and cutting depth to avoid work hardening problems.
4. Use advanced CNC processing technology
Use five-axis CNC processing to reduce the number of clamping times and improve processing accuracy.
Combined with CAD/CAM programming, optimize tool paths and reduce processing time.
Conclusion
The combination of stainless steel investment casting and CNC machining provides an ideal solution for the production of high-precision and complex parts. Investment casting can efficiently produce parts with complex shapes, while CNC machining can further improve accuracy and functionality. By optimizing the design, reasonably selecting materials, and using advanced tools and processing technology, manufacturing efficiency can be greatly improved to meet high-demand applications in different fields.
In the future, with the development of intelligent manufacturing technology, the combination of investment casting and CNC machining will be further optimized to provide better solutions for high-end manufacturing!
Tianhui Machine has the capabilities of stainless steel investment casting and CNC machining, and we can help you choose the right manufacturing method for your project. If you have any questions about your stainless steel investment casting or CNC machining projects, please feel free to contact us!
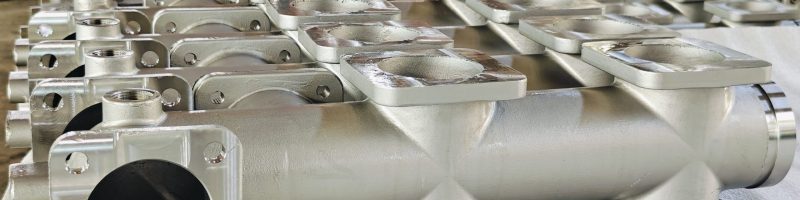
Work with us on your project
Looking for a reliable foundry partner like Tianhui Machine? Send your CAD drawings and 3D files to info@cn-tianhui.com for a quick quote!