Why Is Stainless Steel Difficult to Machine?
Stainless steel is a material known for its strength, durability, and corrosion resistance. These properties make it a top choice for a variety of industries, from aerospace to medical devices to automotive parts. However, despite its many advantages, CNC machining stainless steel still presents significant challenges. In this blog post, we will explore the main reasons why stainless steel is difficult to machine and how engineers and machinists can overcome these challenges.
1. Hardness and Toughness
One of the primary reasons stainless steel is tough to machine is its inherent hardness and toughness. Stainless steel is made up of a combination of iron, chromium, and other elements such as nickel, molybdenum, and sometimes titanium. These elements contribute to the alloy’s strength and hardness, but they also make it harder for cutting tools to cut through the material effectively.
While the alloy is resistant to corrosion and wear, its hardness can cause significant wear on cutting tools. As tools come into contact with the stainless steel, the intense friction generates heat, which can cause tool degradation and even tool failure over time. In many cases, machinists must use high-quality, heat-resistant cutting tools like carbide to effectively machine stainless steel, which can be expensive.
2. Work Hardening
Another key challenge when machining stainless steel is its tendency to work-harden. Work hardening occurs when the material undergoes deformation (due to machining or processing), causing the metal’s hardness to increase in the area directly affected by the cutting process.
As a result, the material becomes harder and harder the more you machine it. This can make the cutting process progressively more difficult, resulting in increased tool wear, reduced cutting efficiency, and the need for frequent tool changes. In addition, if the cutting process generates excessive heat, the material will work-harden even faster, compounding the problem.
To combat this, machinists often employ slower cutting speeds, appropriate coolant use, and sharp tooling to minimize heat buildup and avoid excessive work hardening.
3. High Heat Generation
Stainless steel has a relatively low thermal conductivity, meaning that it does not dissipate heat as efficiently as other metals like aluminum or copper. When machining stainless steel, the heat generated during the cutting process tends to accumulate at the cutting zone rather than being spread out across the material. This can result in higher cutting temperatures, which can affect both the machinist’s tools and the quality of the finished product.
High temperatures can cause several problems, including thermal expansion of the material, leading to dimensional inaccuracies. The heat can also lead to tool wear or even failure if not managed correctly. To manage heat buildup, machinists often use coolant or lubricant to keep temperatures within a manageable range and to avoid overheating.
4. Chip Formation and Removal
The process of chip formation is also a concern when machining stainless steel. Stainless steel produces long, stringy chips that can be difficult to manage. These chips tend to adhere to the cutting tool and the workpiece due to the material’s high strength and toughness, which can cause several issues, such as:
Clogging the cutting area: Long chips can pile up in the machining area, obstructing tool paths and creating additional heat buildup.
Damage to the workpiece: If chips are not properly removed, they can scratch or damage the surface of the workpiece, compromising its final quality.
Tool damage: Adhesion of chips to the cutting tool can result in premature tool wear.
To mitigate these issues, it’s essential to employ the correct chip-breaking techniques and use appropriate coolant or lubrication to help the chips break into smaller, more manageable pieces.
5. Varied Grades and Compositions of Stainless Steel
Stainless steel is a versatile material, and it comes in a wide range of grades, each with different mechanical properties. Some grades, such as 304 stainless steel, are more ductile and easier to machine, while others, like 17-4 PH or 416 stainless steel, are much harder and more challenging to machine.
The specific alloy composition affects how the material behaves during machining, meaning that what works for one type of stainless steel may not work for another. When working with a specific grade, machinists need to carefully adjust their techniques, cutting speeds, and tool selection to achieve the best results.
6. Tendency to Gall and Stick
Gall and stick, a form of material buildup, is a particular concern when machining stainless steel. The material’s high strength, combined with its tendency to work-harden, can cause the tool to become “sticky” with the metal. This leads to material buildup on the cutting edge, which can further degrade the tool and affect the quality of the machined part. This is particularly a concern when machining at high speeds or with dull tools.
Proper lubrication, using cutting fluids, and ensuring tools are sharp are essential steps in preventing galling and sticking during machining operations.
Overcoming the Challenges of Machining Stainless Steel
While stainless steel can be difficult to machine, it is far from impossible. Skilled machinists and engineers use a range of strategies to tackle the challenges presented by this material:
- Use High-Quality Cutting Tools: Carbide and high-speed steel (HSS) are common choices for machining stainless steel. These materials are more heat-resistant and capable of withstanding the stress required to machine the material effectively.
- Optimize Cutting Parameters: Proper selection of cutting speeds, feeds, and tool geometry can help minimize heat generation and reduce the risk of tool wear. Slower cutting speeds and deeper cuts can also help prevent work hardening.
- Use Coolants and Lubricants: Coolants and lubricants help manage the heat generated during the cutting process, reducing thermal expansion and work hardening. They also help with chip removal and prevent tool wear.
- Select the Right Grade: Understanding the specific grade of stainless steel you are working with is crucial. Some grades may be easier to machine than others, and selecting the correct grade for the application can significantly improve the machining process.
- Tool Maintenance: Regularly inspecting and replacing worn-out tools ensures that cutting edges remain sharp, which reduces the risk of galling and sticking.
Conclusion
Machining stainless steel requires a comprehensive understanding of the material’s properties and challenges. Its hardness, work-hardening tendency, high heat generation, and chip formation issues all contribute to making it a difficult material to machine. However, with the right tools, techniques, and a thoughtful approach, these challenges can be overcome, allowing machinists to produce high-quality parts from this versatile and durable material. By applying the best practices for cutting, cooling, and tooling, professionals can ensure they achieve efficient, precise results when working with stainless steel.
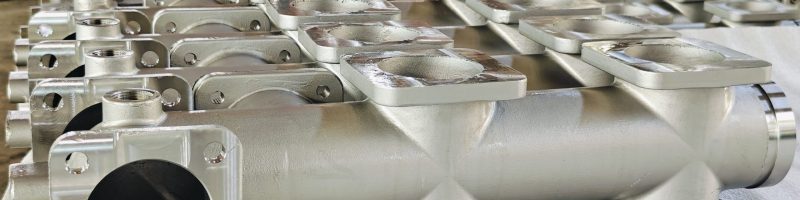
Work with us on your project
Looking for a reliable foundry partner like Tianhui Machine? Send your CAD drawings and 3D files to info@cn-tianhui.com for a quick quote!